NEWS
News
Related News
Key points for selecting and maintaining rubber rollers, the film-coated rubber roller manufacturer will explain for you.
Release time:
2025-01-23 16:14
Coated roller manufacturerIt is believed that the performance and management level of the rubber roller, as an important stretching component, are closely related to the quality of the yarn. Manufacturers should not only pay attention to the manufacturing process and grinding precision but also the subsequent use, management, and maintenance of the rubber roller are very important to ensure the excellent and stable spinning performance of the rubber roller. Only by complementing each other can a stable yarn quality level be achieved.
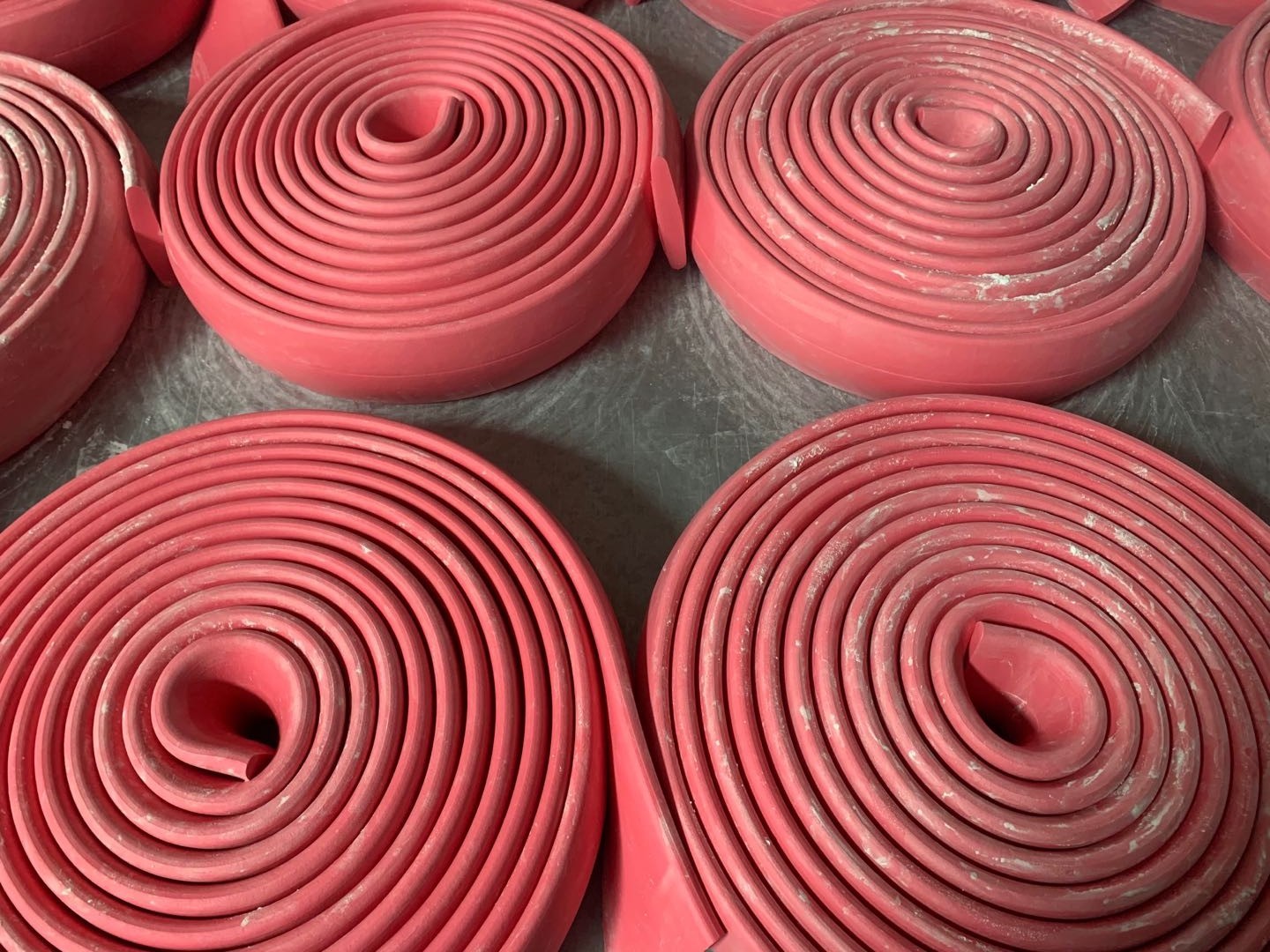
The coated roller manufacturer believes that before bulk purchasing rubber hoses (including new hoses or selecting new hose manufacturers), one should understand the model, specification, performance, and yarn quality of the selected hoses. Specific methods include:
1) Since there are many manufacturers producing rubber hoses in China, with a wide variety, it is essential to first understand the manufacturers;
2) The coated roller manufacturer believes that the hardness of the rubber hoses ranges from Shore A 60 to 90 degrees, so before purchasing hoses, one should understand the manufacturer's manufacturing process and have a certain understanding of the manufacturer's equipment condition and technical level;
3) Conduct small batch tests and carry out pilot tests under the premise of stable yarn quality;
4)Coated roller manufacturerIt is believed that when purchasing in large quantities, at least one position should be tested to fully understand its lifespan fluctuations, trial spinning performance, and variety applicability. The rubber roller operates in different seasons (especially in high temperature and high humidity seasons), testing the anti-winding, wear resistance, elastic recovery, and permeability of chemical coatings, etc. Only after passing the tests can it be promoted on a large scale.
The coated roller manufacturer believes that after the new rubber rollers arrive, they should be strictly accepted according to relevant standards and regulations, and acceptance records should be filled out. Inspection items include: model, geometric size, correctness of outer packaging marks, correctness of hose marks, consistency of surface color, uniformity of hardness, good elasticity, absence of cracks and delamination, uniform wall thickness, good roundness, etc. After acceptance, establish relevant account cards. Non-conforming products should be handled as follows: 1. All non-conforming products should be counted and returned by the supply department; 2. According to the requirements of sampling inspection, it is strictly forbidden to return entire batches that do not meet standards, and the use of non-conforming products on passenger vehicles is prohibited.
The coated roller manufacturer believes that several issues should be noted in the production of rubber rollers.
1) Calculate the procurement quantity of rubber hoses in advance, reserve spare parts, and load the entire batch at the same time.
2) The outer chamfer of the bearing should be 20 ~ 30, and the ribs and fine thread should be equidistant. If the outer chamfer is 45, it is easy to damage the inner hole of the aluminum-lined hose during the sleeve-making process; non-aluminum-lined hoses can use 45.
3) The coated roller manufacturer believes that if the grinding machine's holder is a rubber roller honed in the middle position, the bearing core should be produced by a centerless grinding machine; a simple way to identify a sand core produced by a centerless grinding machine is to look at both ends of the sand core, which should not have top holes.
4) Check whether the bearing is flexible, whether there is oil contamination, whether the bearing gap is appropriate, and whether there are any scratches or debris on the bearing surface.
5) When making rubber rollers, try to choose vertical rubber rollers, adjust the centerline properly, maintain moderate pressure, check whether the rubber roller probe is worn, and regularly maintain and adjust the equipment.
6) After the sleeve system is completed, check whether there are metal shavings at both ends of the bearing, and if so, clean them up in a timely manner.
7) When oiling and pressing the cover, special tools should be used to avoid blocking oil at both ends.
8) The coated roller manufacturer believes that the shaft core should be oiled appropriately, and oil should be replenished after 4 months of use.
Rubber-plastic alloy rubber, printing mixed rubber manufacturer, rubber roller manufacturer, film-coated rubber roller manufacturer
Related News