NEWS
News
Related News
Supplier of compounded rubber: Factors affecting the compounding process
Release time:
2025-01-23 16:14
1. Raw materials prepared for the previous process: The quality of natural rubber, carbon black, oils, and additives directly affects the mixing effect and the quality of rubber materials. ThereforeMixing Rubber SupplierThe mixer should supervise the previous process to ensure the quality of the mixture.
2. Feeding sequence: A reasonable feeding sequence is conducive to uniform mixing. If the feeding sequence is inappropriate, it will affect the uniformity of dispersion to a lesser extent, leading to clumping or excessive refining, even coking, making the next operation difficult and reducing the performance of rubber materials. Therefore, mixing rubber suppliers need to add materials according to the time and order specified in the process regulations.
3. Mixing temperature: During the mixing process, the mixing temperature of natural rubber is generally controlled around 130°C, and the discharge temperature is generally controlled within the range of 130~145°C. If the temperature is too low, it often causes the rubber material to not clump under pressure; if the temperature is too high, it will soften the rubber, weaken the mechanical shear effect during stirring, and be detrimental to the dispersion quality of fillers. Therefore, mixing rubber suppliers should pay attention to controlling and adjusting the cooling water or heating steam according to process requirements to control the temperature of the mixing chamber.
4. Mixing time: Generally, feeding and stirring need to be strictly carried out according to the time required by the process regulations. ForMixing Rubber Supplierthe same production machine, if the mixing time is short, the formulation will be uneven, the plasticity of the rubber material will be uneven, and the physical and mechanical properties will be uneven; if the stirring time is too long, it is easy to produce "over-stirring" phenomenon, leading to a decline in the physical and mechanical properties of the rubber.
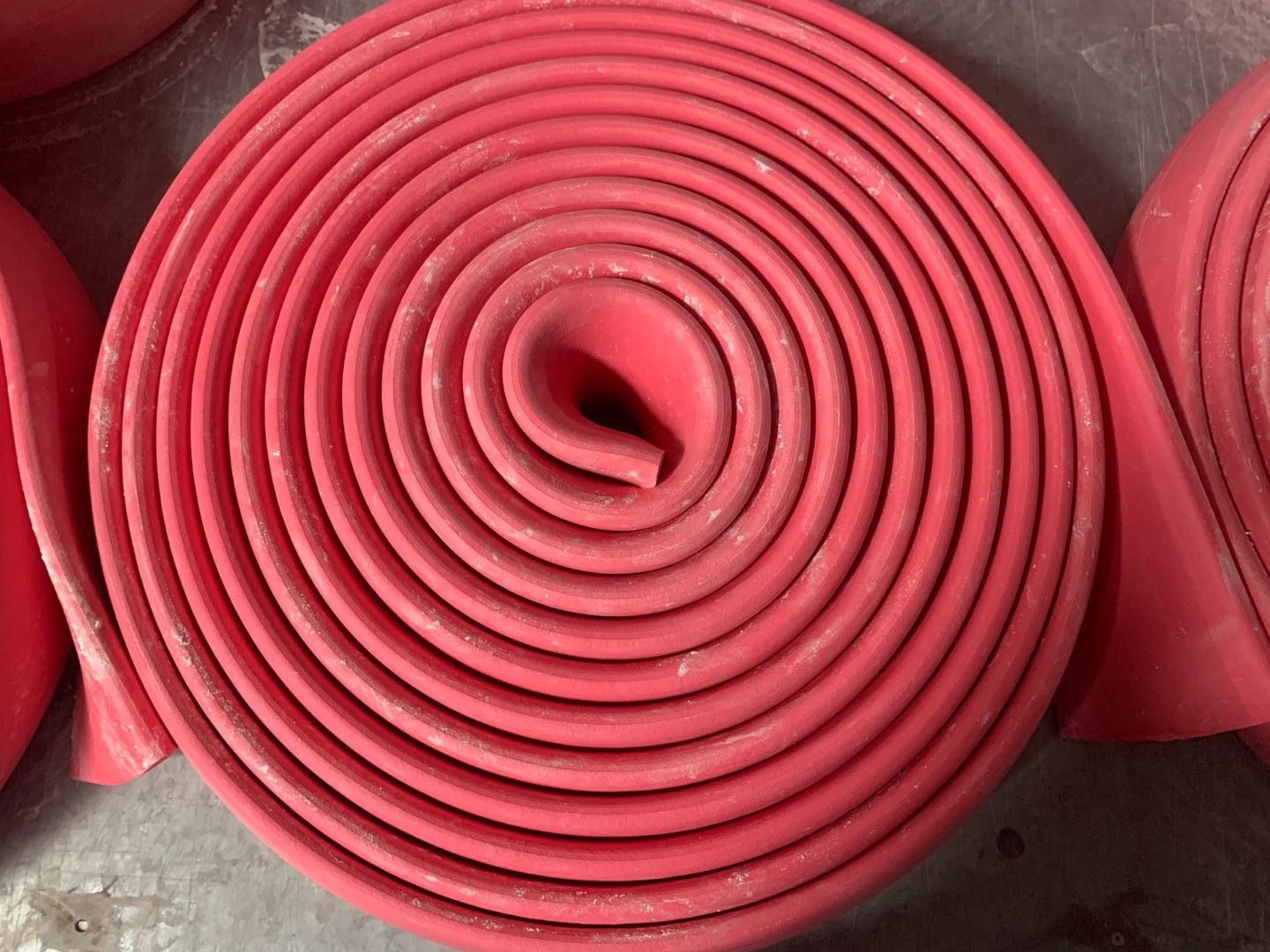
During the feeding process, special attention should be paid to two important times, namely the time for adding oil and the time for adding post-accelerators. Oil addition time: If oil is added too early, carbon black will not mix sufficiently and is prone to agglomeration, leading to poor dispersion and significant fluctuations in physical and mechanical properties; if oil is added too late, the oil will be unclean, and the inner rubber will slip, resulting in poor mixing.Mixing Rubber SupplierIt is recommended that everyone add oil as soon as possible while ensuring the dispersion of carbon black.
5. Pressure: Properly increasing pressure can not only increase the loading capacity of rubber, preventing the phenomenon of loose material during discharge, but also allow the rubber material to contact and squeeze with the equipment and inner rubber material more quickly and effectively, accelerating the process of mixing agents entering the rubber, thereby shortening the mixing time and improving mixing efficiency. If the pressure is insufficient, it will float, creating dead corners at the feed inlet and chamber wall under pressure, where the rubber material cannot be mixed. Mixing rubber suppliers inform that excessive pressure can cause a sharp increase in mixing temperature, which is detrimental to the dispersion of compounds, leading to a decline in compound performance and increased power consumption.
6. Loading capacity: The loading capacity directly affects the quality of the compound. If the capacity is too large or too small, it will prevent the rubber material from being sufficiently sheared and kneaded, resulting in uneven mixing of vulcanized rubber and fluctuations in physical and mechanical properties. Therefore, mixing rubber suppliers need to consider the total loading capacity based on the filling coefficient F of the mixer. For more information about mixing rubber suppliers, please refer to Feiyue New Materials.
Environmental protection rubber roller glue, rubber-plastic alloy rubber, printing compound rubber manufacturer, compound rubber supplier
Related News