NEWS
News
Related News
A one-minute explanation by the rubber compound supplier about what rubber compound is.
Release time:
2025-01-23 16:14
The so-called mixing rubber refers to a type of uncrosslinked rubber that has fluidity, where the compounding agents are mixed from block, granular, and powdered raw rubber.Mixing Rubber SupplierIt is said that the rubber material mixed from raw rubber or plasticized rubber according to the formula and compounding agents using a rubber mixing machine is called mixing rubber. The mixing rubber supplier indicates that mixing rubber is mainly used for automotive parts, front and rear spindle oil seals, front and rear crankshaft oil seals, power steering pump seals, transmission pump seals, dust covers, power steering hoses, and 175-degree radiator hoses.
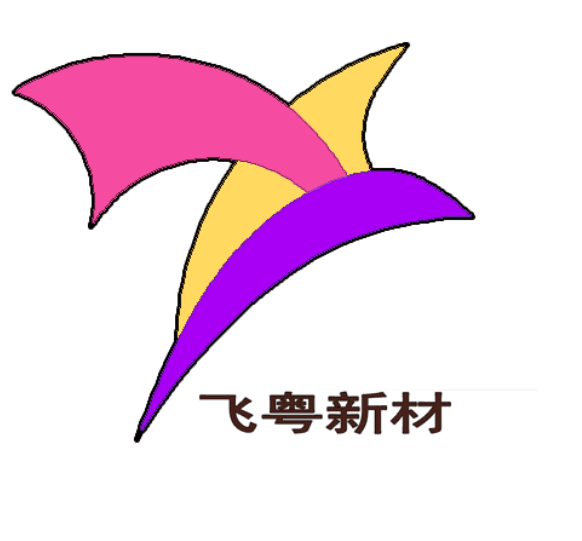
The mixing rubber supplier states that mixing rubber is the raw material for manufacturing rubber products, that is, semi-finished products. Therefore, the quality of the colloidal dispersion directly relates to the quality of the finished product. At the same time, the viscoelasticity and rheological properties directly affect the processing performance and the forming, extrusion, calendering, and other processing techniques in later production.
I. Types of Mixing Rubber
1. Model Vulcanized Mixing Rubber
It is a rubber mixture that is simultaneously formed and crosslinked in a mold. They are suitable for the molding, transfer molding, and injection molding of silicone rubber to prepare automotive seals, gaskets, O-rings, spark plugs, and tire pads, as well as products like electronic buttons and pressure cooker washing machines. This mixing rubber is made from methyl vinyl silicone rubber raw rubber, reinforcing fillers (fumed silica, precipitated silica), semi-reinforcing fillers (diatomaceous earth), incremental fillers (quartz powder), structural control agents, modified additives, and vulcanizing agents. By changing the formula, it can also be made into general-purpose, heat-resistant, and non-two-stage vulcanized mixing rubber.
2. Extrusion Molding Mixing Rubber
Mixing Rubber SupplierIt is indicated that the rubber material for extrusion is usually made from methyl vinyl silicone rubber raw rubber, fumed silica, and other additives. By adding DCBP, hoses, tapes, and wires can be made using an extruder and hot air vulcanization process. Extrusion compounding requires a certain degree of plasticity. When using a grade with too low hardness, the plasticity of the rubber is too low, making it prone to stickiness, bubbling, and mold release expansion, with the extrudate diameter exceeding the mold diameter too much, affecting the extrusion process and product appearance. Conversely, if a grade with too high hardness is used, it will be difficult to extrude due to the small mold expansion. The applicable hardness (Shore A) is 50-70. Precipitated silica with high moisture content is not suitable as a reinforcing filler for extrusion molding silicone rubber, otherwise, it is prone to foaming during hot air vulcanization.
II. Characteristics of Mixing Rubber
1. General technical content;
2. High Price;
3. Simple processing equipment.
4. Wastes labor, the working temperature of the molding machine is high, harmful to workers' health, and not conducive to long-term operation by workers;
5. Complex processing procedures (mixing with vulcanizing agents, mixing colors, slicing, manual weighing);
6. Can be fully automated controlled, with a scrap rate of less than 1%.
Printing compound rubber manufacturers, compound rubber suppliers, UV special water roller rubber, printing compound rubber
Related News