NEWS
News
Related News
The process and characteristics of compound rubber, as told by the compound rubber manufacturer.
Release time:
2025-01-23 16:14
Compound RubberThe manufacturer believes that mixing is the process of using the mechanical force of a rubber internal mixer to evenly disperse various compounding agents in the rubber. The mixing process is to evenly disperse various compounding agents in the rubber, forming a mixture with rubber as the medium or a mixture of rubber and some compatible components (compounding agents and other polymers) as the medium, and a multiphase colloidal dispersion system with incompatible compounding agents (such as powder fillers, zinc oxide, pigments, etc.) as the dispersed phase.
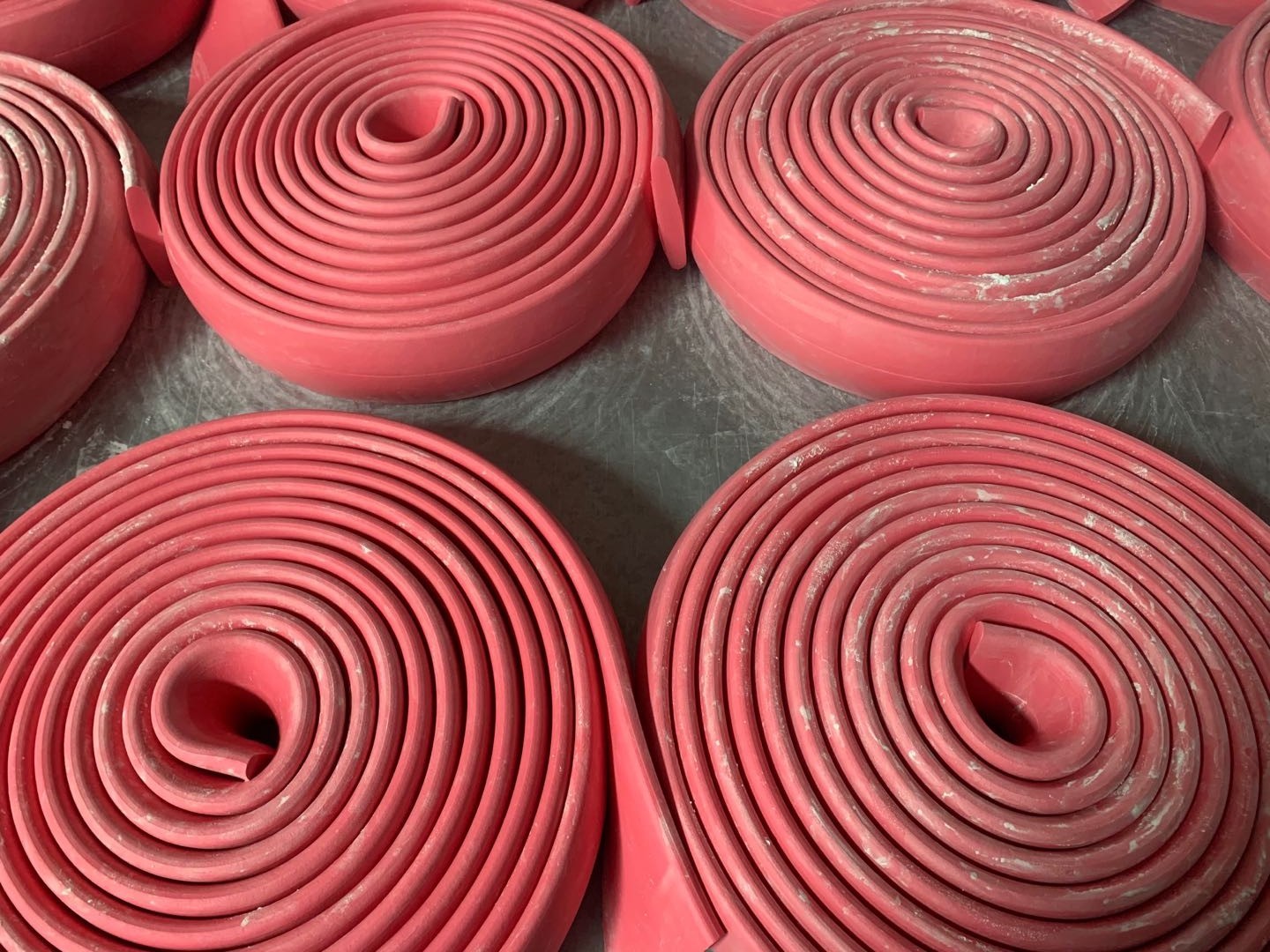
The manufacturer of compound rubber believes that the specific technical requirements of the mixing process are: the compounding agents must be evenly dispersed, especially the reinforcing compounding agents such as carbon black must achieve a good degree of dispersion to ensure the consistency of rubber performance. The rubber material obtained after mixing is called "compound rubber," and its quality has a significant impact on further processing and product quality. The necessary condition for open mixing is to select the appropriate roller temperature (as shown in the table below) based on the basic properties of various rubbers, such as viscoelasticity, relaxation time, transition temperature, etc., to keep it in a roller-wound state for mixing.
Compound RubberThe manufacturer believes that the feeding order is an important factor in improving the mixing quality of the open mill. An improper feeding order can lead to uneven dispersion, rolling of the rubber, excessive refinement, and even early vulcanization (scorching) and other quality issues. In principle, the feeding order should be determined based on the characteristics and dosage of the compounding agents in the formulation, prioritizing those with a small dosage and difficult dispersion. After adding a large amount, it is easy to disperse; finally, sulfur or highly active, low critical temperature accelerators (such as super-speed accelerators) should be added to prevent early vulcanization (scorching). Generally, liquid softeners are added after mixing powder fillers such as reinforcing fillers to prevent powder agglomeration, rubber slippage, rubber softening, leading to low shear force and difficulty in dispersion.
The manufacturer of compound rubber believes that in addition to the impact of roller temperature and feeding order on the mixing quality of the open mill, attention should also be paid to: the rubber filling amount should not be too much, otherwise it will be difficult to mix evenly; the capacity of synthetic rubber should generally be less than that of natural rubber. Under the premise of ensuring mixing quality, the mixing time should be shortened as much as possible to prevent the physical and mechanical properties of the compound rubber from declining due to over-mixing, affecting production efficiency. The roller speed and speed ratio should be appropriate, which is conducive to mixing and dispersion, and will not cause early vulcanization (scorching) due to excessive heat generation.
The manufacturer believes that the internal mixer generates complex flow patterns and high shear forces through the rotors and upper and lower bolts in the mixing chamber, allowing rubber compounding agents and granular additives to be quickly crushed and evenly dispersed. This is an effective mixing method. However, high shear forces can cause the material temperature to rise rapidly during the mixing process, generally reaching 130 degrees. This exceeds the activation temperature of most vulcanization systems, which will lead to early vulcanization (scorching) of the rubber material.
Compound RubberThe manufacturer believes that the general practice is to mix most of the materials in the internal mixer, and then discharge the rubber from the internal mixer to the open mill, adding vulcanizing agents or super-speed accelerators in the open mill. In fact, the open mill only squeezes the rubber material in the roller gap, providing a large cooling area, resulting in a decrease in material temperature. Adding vulcanizing agents at this stage can avoid premature vulcanization (scorching) of the rubber material.
Rubber roller mixing rubber, mixing rubber manufacturer, printing mixing rubber manufacturer, mixing rubber supplier, mixing rubber
Related News