NEWS
News
Related News
Some knowledge points about polyurethane blended rubber, explained by the blended rubber manufacturer.
Release time:
2025-01-23 16:14
PolyurethaneMixing rubberIt is a type of mixed polyurethane rubber (referred to as MPU) synthesized from polyether polyol and methylene diphenyl diisocyanate (MDI) as the main raw materials, which has an unsaturated structure. The vulcanization system can choose peroxide or sulfur. The processing technology and vulcanization molding process and equipment are the same as those of general rubber; it is suitable for manufacturing rubber products with hardness ranging from Shore A 50 to 95.
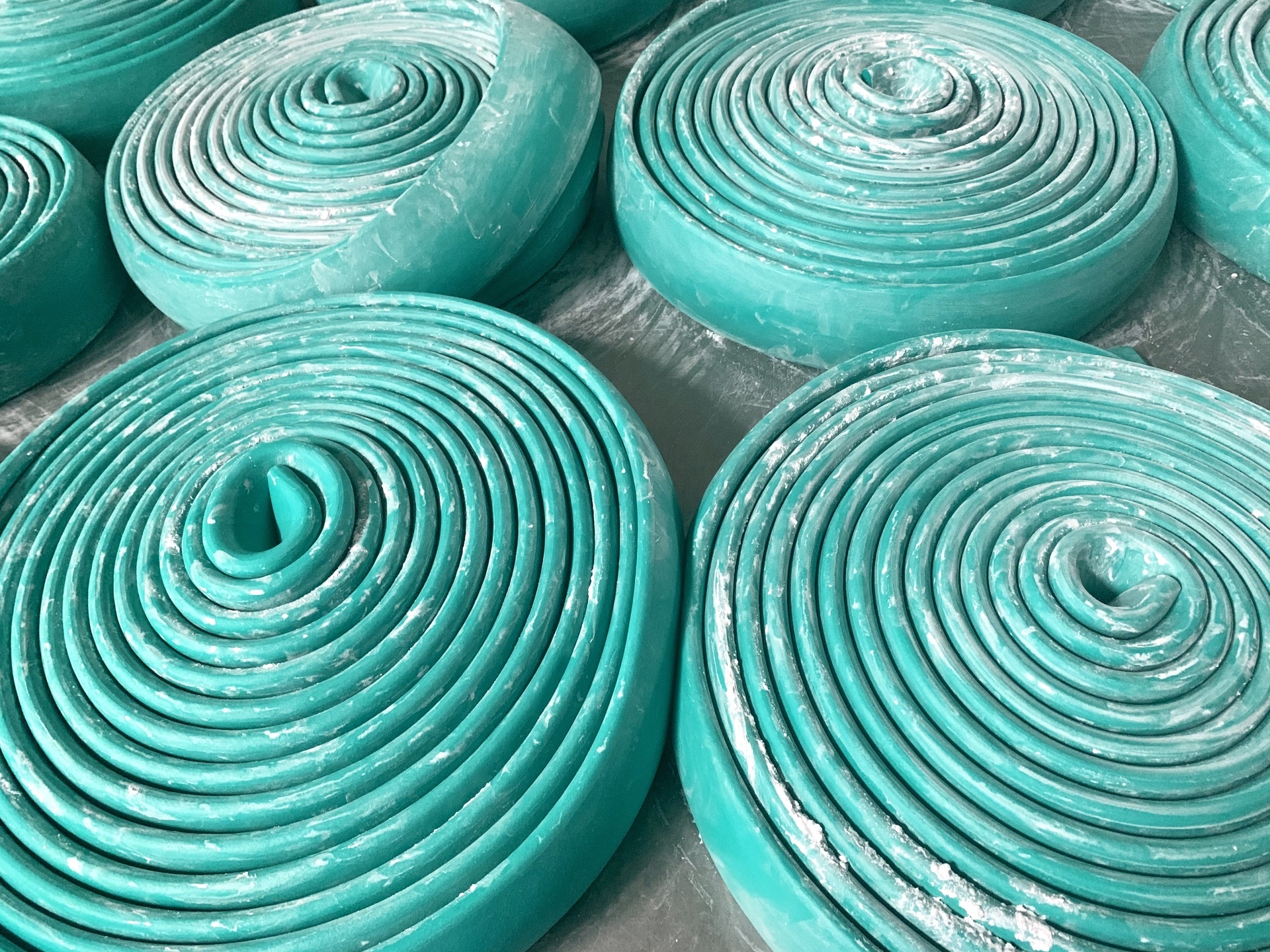
PolyurethaneMixing rubberIt has good wear resistance, oil resistance, aging resistance, ozone resistance, radiation resistance, hydrolysis resistance, low-temperature resistance, and good processing performance. Mixed polyurethane can be used in many industrial fields, including machining and equipment manufacturing, textile industry, petroleum industry, transportation, and automotive industry. Typical application fields include tile molds, hydraulic gaskets, diaphragms, seals, tapes, rubber roller coverings, O-rings, shock absorbers, pump stators, cable sheaths, sandblasting hoses, and shoe soles.
1. Oil-resistant sealing products. The mixing rubber manufacturer believes that the temperature range for peroxide-vulcanized rubber is -40 to 100, with a long-term use temperature of 80. It can be used to make various oil-resistant and emulsification-resistant seals.
2. Buffering and shock-absorbing products. Polyurethane rubber vulcanized with sulfur or peroxide has buffering and shock-absorbing properties and can be used to make various shock-absorbing pads.
3. Wear-resistant transmission products. Sulfur-vulcanized polyurethane rubber has wear resistance, airtightness, and ozone resistance, making it suitable for making various shaft sleeves, conveyor belts, and tracks.
The mixing rubber manufacturer believes that a reasonable amount of rubber should ensure friction and shear in the mixing chamber and allow for even dispersion of the additives. The amount of rubber is determined by the equipment and the characteristics of the rubber mixture. If the equipment has been used for a long time, due to wear of the mixer, the filling coefficient can be larger, and the filling amount can be increased. For example, if the pushing pressure is large or the plasticity of the rubber mixture is high, the amount of rubber can also be increased accordingly.
Mixing rubberThe manufacturer believes that increasing the pushing pressure can not only increase the loading capacity of the rubber material but also allow the rubber material to contact and extrude the internal equipment and components more quickly and effectively, accelerating the mixing process of the additives into the rubber, thereby shortening the mixing time and improving production efficiency. It can also reduce the sliding of materials on the contact surfaces of the equipment, increase the shear stress of the rubber material, improve the dispersion of the additives, and enhance the quality of the rubber material. Therefore, many measures have been taken to improve the mixing efficiency of the internal mixer and the quality of the rubber material, such as increasing the diameter of the top bolt gate or increasing the air pressure.
The mixing rubber manufacturer believes that during the mixing process, the shear speed of the rubber mixture is proportional to the rotor speed. Increasing the shear speed of the mixing rubber can shorten the mixing time, which is the main measure to improve the efficiency of the internal mixer. To meet the requirements of the mixing process, multi-speed or variable-speed internal mixers have been adopted for mixing, allowing the speed to be changed at any time according to the characteristics of the rubber material and process requirements to achieve better mixing results.
The mixing rubber manufacturer believes that the structure and shape of the internal mixer rotor have a significant impact on the mixing process. The convex ribs of the elliptical rotor of the internal mixer have increased from two to four, which can more effectively perform the functions of shearing and stirring. This can improve production efficiency by 25-30% and reduce energy consumption. In recent years, in addition to elliptical rotors, other triangular and cylindrical rotors have also been applied in production.
Rubber roller compound, compound manufacturer, printing compound manufacturer, compound
Related News